Dynetics completes critical hardware demonstrations for sustainable human landing system
Dynetics, a branch of the Leidos enterprise, has successfully completed more than a dozen hardware tasks on its sustainable human landing system (HLS) program over the past 17 months. Those tasks, which include design, build and test of critical technologies, lay the groundwork for development of the complete lander system.
“Our team has continued to work hard over the past couple of years to mature our design and build on lessons learned,” said Andy Crocker, program manager for HLS at Dynetics. “We’ve been fortunate to be able to demonstrate so many key technologies for our lander with full-scale hardware in relevant environments.”
Dynetics was one of five companies selected in September 2021 to collaborate with NASA to mature lander designs and conduct risk reduction activities in support of sustainable lander development for its Artemis program. These efforts are preparing industry for the HLS Sustaining Lunar Development (SLD) program, which NASA will use to fund the development of a second HLS.
Recent demonstrations included technical areas such as propulsion, cryogenic fluid management, lunar dust mitigation, power and docking systems.
Propulsion
The largest number of tasks were focused on propulsion—for the main engines, reaction control system (RCS), and overall propulsion system.
Dynetics’ propulsion system runs on oxygen and methane, which are used in their liquid form for the main engines and as gases in the reaction control system (RCS). After developing a dual regen chamber (meaning the chamber is cooled using both propellants), hot fire tests were conducted at Marshall Space Flight Center (MSFC) with a full-scale chamber, generating critical data for main engine development.
Full-scale main engine turbopumps were also built, then operated in water and cryogenic fluids to verify their rotordynamic characteristics. Flow throttling was demonstrated with a turbine bypass valve at MSFC’s Component Development lab, and ways to control vaporization of cryogenic propellants for use in the RCS with a low mass design were tested.
The RCS thruster development team conducted over 500 tests, including vacuum testing with a full-scale refractory metal nozzle, to refine the RCS design.
“We have an outstanding propulsion team at Dynetics,” said Robert Wright, space division manager. “Combining our expertise with NASA Marshall’s, we were able to develop a propulsion system that is ideal for HLS missions.”
Cryogenic Fluid Management
The transfer of cryogenic fluid from one spacecraft to another has never been done in space before, but this complex swap is required for all current HLS proposals – be it in Earth’s orbit or around the moon. While it wasn’t possible to test its idea in space, Dynetics was still able to successfully demonstrate a fast transfer of cryogenic fluid to a full-scale tank.
“This really heightens our confidence in our propellant transfer approach, which is vital to reducing the risk of our lander architecture,” Crocker said.
Using the same full-scale tank, the team incorporated testing of radio frequency mass gauging (RFMG) technology, which was developed at NASA Glenn Research Center. RFMG measures total mass of a two-phase fluid in microgravity. Initial data showed incorporating the technology into lander development looked promising.
Transferring of cryogenic fluids is important, but so is preventing leaks. Leak prevention can be difficult due to the frigid temperatures of cryogens. Dynetics completed demonstrations of its approaches to minimizing leakage at cryogenic temperatures from sealing interfaces for periodic-use components like umbilicals as well as long-term use such as valves. The results will guide future design decisions.
Lunar Dust Mitigation
During the Apollo missions, moon or lunar dust was a difficult problem for astronauts. Lunar dust is clingy and not easily brushed off surfaces once it attaches, unlike dust on Earth. For the longer duration missions planned for Artemis, there is concern that buildup of lunar dust could render critical components—like solar arrays and cameras—unusable.
A promising solution initially developed at NASA Kennedy Space Center is called an Electrodynamic Dust Shield (EDS). This technology uses electrical charges via tiny wires built into surfaces such as optical lenses to remove dust quickly and efficiently. Dynetics manufactured EDS devices and showed they can greatly mitigate the buildup of dust on critical surfaces.
“Our unique micro-fabrication skills made EDS a perfect fit for us,” said Wright. “We managed to advance the technology beyond what the team originally planned.”
Power
For power, Dynetics focused on two key objectives: demonstrating that high power density batteries can meet NASA’s stringent standards for human missions and defining a feasible, near-term approach to provide energy to the lander during lunar darkness. The team conducted thermal runaway tests of advanced batteries at cell and module levels to prove viability for space flight. The team also developed an innovative approach to operate the lander through a 14 Earth-day-long lunar night and demonstrated the central enabling technology.
“As alluring as the moon is as a destination, it is an unforgiving environment for humans,” Crocker said. “Designing a lander with technology that can eventually help us not only survive but sustain a presence on the lunar surface takes all the ingenuity we can muster as a team. But we believe our lander will be both safe and affordable for HLS.”
Docking Systems
Finally, Dynetics is developing a commercial spacecraft docking system, which will be applicable to HLS, Gateway, commercial space stations, and other systems. Demonstration of the system took place in a full-scale kinematic testbed at a wide range of simulated condition, paving the way for detailed design and qualification.
“The team has achieved fantastic results,” said Crocker. “We will continue to mature our technology and reduce risks for lander development as we prepare for the next contract.”
History
Dynetics has been an HLS prime contractor for more than three years. It was awarded contracts in 2019 and 2020 under NASA’s Next Step Space Technologies for Exploration Partnership (NextSTEP-2) program. In December, the company announced it had selected Northrop Grumman, the only company to build a successful Moon lander, as a part of its team for a recent bid on NextStep-2 Appendix P.
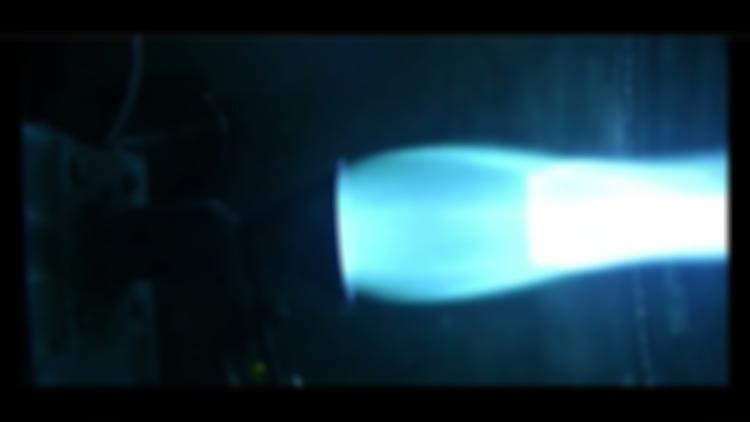